cGMP Manufacturing
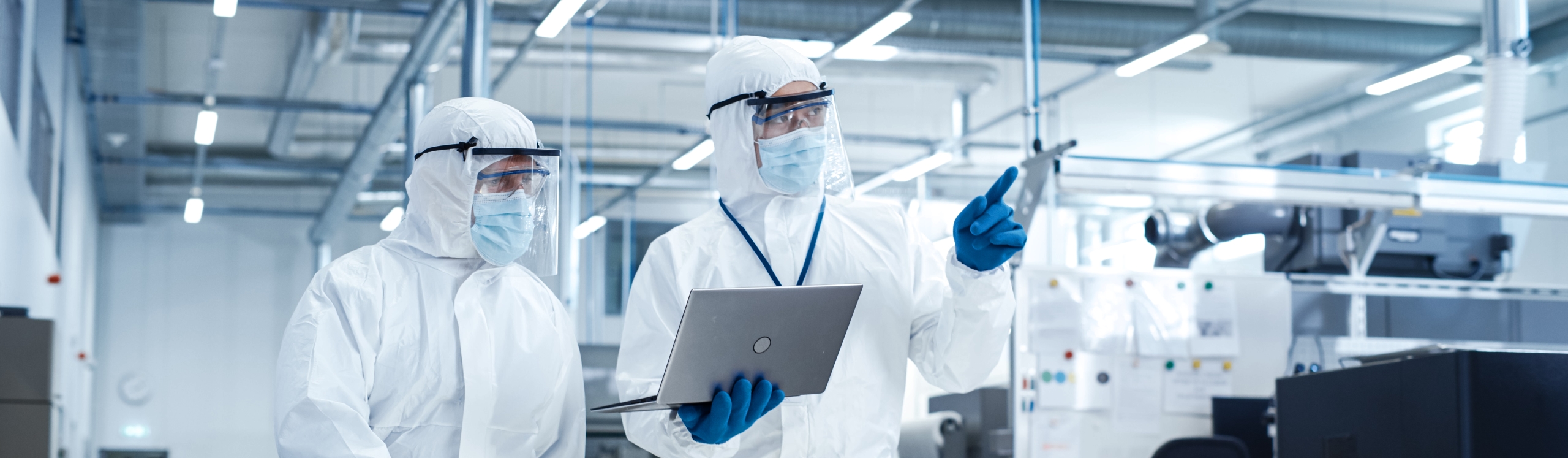
Reliable Manufacturing Solutions
Aligned with cGMP Standards
Manufacturers of pharmaceuticals and medical devices require cGMP-compliant manufacturing software. Slingshot Pharma’s Manufacturing Execution System (MES) application meets this requirement. From work order creation through component allocation, the staging and work order completion of all transactions are carefully tracked and audited. Electronic signatures are required at critical stages of the work order workflow process including:
- Creation and opening of a work order,
- Completion of certain process steps required of your MES workflow,
- Completing and closing a work order.
Work Order Creation & Adjustments
Work orders are created in the Slingshot Pharma system from a template including a bill of materials, bill of resources and a bill of processes. This information provides an electronic batch record eliminating paper documents. The work order details can be adjusted to substitute valid component materials, change quantity relationships or remove optional component material. All changes are audited at the field level. The audit trail includes the reason for the change, the before and after values of the fields changed, the user who made the change and the date and time of the change.
Component material lots can be specified manually prior to opening the work order or automatically as material staging tasks are created. Automatic allocation options include FEFO (first expiration, first out) and FIFO (first in, first out). Material can be staged in the work cell (e.g. cleanroom) or in an adjacent location. Material allocations are confirmed before the work order begins.
Work Order Completion
Upon work order completion, the remaining quantities of each component can be adjusted to accurately reflect and account for yield variances. Lot numbers are assigned to the completed item and labels are printed automatically. Labels can include the product name, GTIN, dosage, batch number, and expiration date. An expiration date can be set manually or automatically assigned based on the standard expiration days parameter for the item manufactured. Genealogy records tracking the lots and equipment used in the process are created automatically.
Work orders can be created manually as described above, or automatically by Slingshot Pharma’s Supply Chain Planning tool.