cGMP Inventory Control
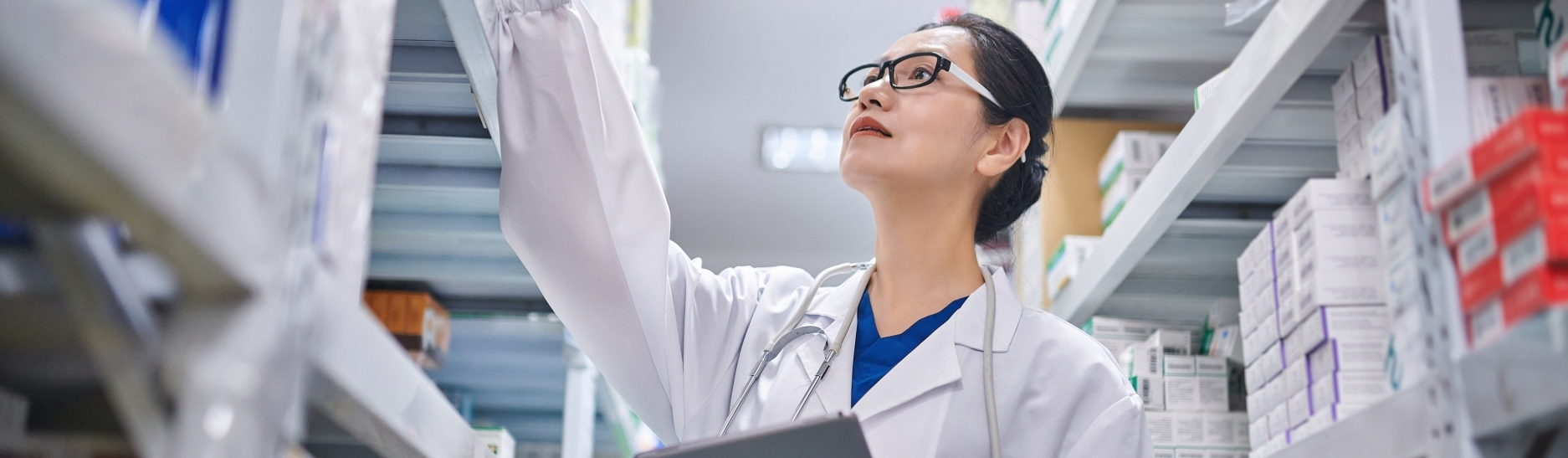
Your Partner in cGMP-Driven
Inventory Control
Pharmaceutical companies mandate lot-based material control. Material status determines the authorized uses of the material. Drug products are received in with a status of “Quarantine”. Certain materials require sampling and testing. When test results are received, the material status is changed by a user from Quality to “Released” or “Rejected”. Rejected materials can be returned to the supplier or forwarded to another department (e.g. Analytical Development) for non-GMP processes or destroyed. Slingshot Pharma’s workflows simplify and audit this process.
To maintain a 21 CFR Part 11-compliant environment, cGMP materials management requires a complete and thorough audit trail. Slingshot provides both “field level” auditing of changes to reference data and a physical inventory transaction log showing all changes to inventory balances. For each transaction, the reason, the user performing the function, and the user signing and date/time are recorded.
cGMP Inventory Control tracks testing and expiry dates on “lot dated” materials. A background process automatically changes the material status to “Expired” when the expiry date is reached. The same process resets the status to “Quarantine” if a retest date is reached. The status updates made via the background processes are captured in the audit trail.
A material item can be stocked in multiple units of measure. Label formats can be specified for each unit. One unit can be designated the “sell unit”. cGMP Inventory Control tracks the range of sell units in each larger packaging unit. Units can be broken down to smaller units or built up to larger units.
Slingshot Pharma’s cGMP Inventory Control supports “cold chain” material control and tracking. Environmental requirements (temperature, humidity etc.) can be set for any material item. Environmental capabilities are set at the warehouse zone level. Logic prevents the user from placing material in a location that does not meet its storage requirements. It may be necessary to stage material outside of its required environment for a brief period of time. When this occurs, Slingshot Pharma alerts the appropriate users if the maximum “time out of temp” is approaching.
Slingshot Pharma’s cGMP Inventory Control allows multiple “owners” of material. This allows Contract Manufacturing Organizations (CMOs) to track inventory separately for each of their customers. In rare cases, ownership can change. The ownership change action will appear in the inventory transaction log and require electronic signature.
Other inventory capabilities include support for Cycle Counting, Equipment Maintenance Workflows, Stock Replenishment (via work orders or purchase orders) and intra-plant Material Transfer Orders.